ISO 9001 | Quality
What is ISO 9001?
As the internationally recognised standard for quality management, ISO 9001 specifies the set requirements for a quality management system (QMS). It focuses on regulating and improving the processes you already have in place to ensure high-quality products and services for your customers as well as staff and other key stakeholders.
While ISO 9001 certification is not a legal business requirement, it is recognised as an important (and sometimes essential!) certification across many industries. It can also be used by any organisation, large or small, regardless of its field of activity to help companies to achieve superior operational performance. It’s for this reason that ISO 9001 certification is widely sought-after.
At Candy Management Consultants, we help you to achieve the latest ISO 9001 registration (2015 version) by implementing and approving simple yet effective quality management systems. So, why not join the one million companies and organisations in over 170 countries that have already achieved their ISO 9001 certification by speaking with one of our consultants today?
Offering flexible payment plans and enjoying a 100% success rate to date, we can provide expert ISO 9001 advice and guidance for a wide range of businesses and corporations.
What are the principles of ISO 9001?
Published by the ISO (International Organization for Standardization – a worldwide federation of national standards bodies), this standard ensures high-quality products and/or services by following a range of different principles including a strong customer focus, the motivation and implication of top management, the process approach and continual improvement strategies.
Additional principles of ISO 9001 include taking a factual approach to decision making and a systematic approach to management. An effective QMS is therefore a collection of processes that ensure, every time they are performed, that the same results are consistently achieved.
Why is it important to regulate quality management?
The regulation of a quality management system benefits both the business itself as well as its customers by streamlining operations and meeting or even exceeding customer expectations. ISO 9001 certification can therefore have a positive impact across an organisation by ensuring an efficient, productive and effective workforce as well as satisfied customers that return time and time again.
Not to mention, many corporations will only choose to work with suppliers that have achieved an ISO 9001 certification as it signals a certain level of customer satisfaction and a dedication to continued improvement. The influential nature of this standard and the fact that it must be independently certified ensures ISO 9001 remains an essential certification for many organisations.
To find out more about the benefits of achieving your ISO 9001 certification, we’ve assembled a comprehensive list of advantages below. Alternatively, you can also get in touch with an ISO 9001 consultant from Candy Management Consultants to discuss how your business specifically can benefit from achieving its ISO 9001 certification.
What are the benefits of ISO 9001?
- Increased profits
- Improved customer satisfaction
- Address business risks and opportunities
- Win more tenders
- Issues are identified and resolved promptly
- Better productivity and efficiency
- Consistent documentation of processes
Why choose Candy as your ISO 9001 consultant?
At Candy Management Consultants, we’ve amassed an experienced team of expert ISO 9001 consultants – each with at least ten years of experience in the ISO and health and safety industries. Thanks to this wealth of knowledge and experience, we can guide you through the process to help you achieve your ISO 9001 certification with ease.
We’re here to every step of the way to answer any questions you may have relating to ISO 9001, so please don’t hesitate to get in touch with our team. When you follow our expert ISO 9001 guidance, you are guaranteed to achieve your ISO certification – we are proud to say we have a 100% success rate to date!
To ensure a high level of customer satisfaction, we also ensure that all our services are provided promptly and delivered within the specified timeframe. Crucially, our set day rate and our payment plans help to keep our prices affordable for businesses of all shapes and sizes. Plus, we’ll never charge you for the days that you don’t use our services.
To discuss your ISO requirements or new management system with our knowledgeable team, please don’t hesitate to get in touch by either calling us on 0161 470 7929 or sending us your enquiry via email at info@candymc.co.uk. Alternatively, if now isn’t a good time, you can always request a call back at a time and date that’s right for you by filling out our online contact form with your contact details and enquiry!
Our 3 Step Process
Tailored to you
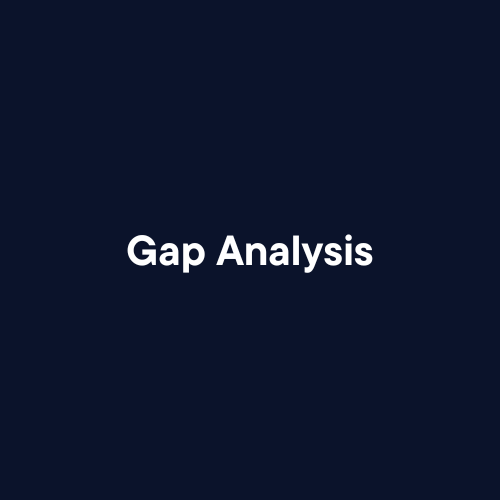
We will complete a thorough gap analysis and review of your business processes to understand how best to implement an ISO compliant management system.
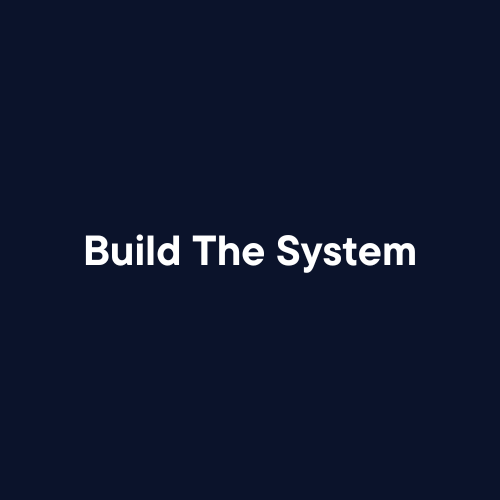
Working with your management team we will build your new management system and where possible align to your existing processes to avoid disruptive change.

We will train your workers on the new system and how to maintain it so that you remain compliant. We will also assist you in your preparation for third-party certification audits.